Dumas
Chris-Craft Cobra pt 2
30 - July - 2016 - 12:43
In the last post, I had just wrapped up the under-planking. Next came the mahogany planking. I began on the keel, running a plank up each side of the center line on the bottom. I also soaked some of the planks, so that they would be easier to bend at the front. Below you can see the darker plank (dark because it is wet), bent around the front of the keel.
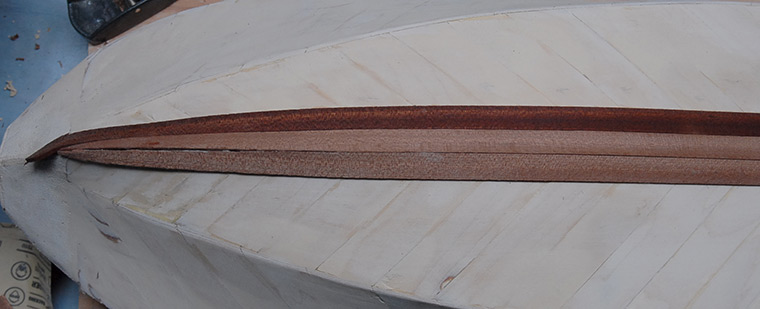
After a few rows of planks from the center, I then added one that runs along the edge that forms the border between the bottom and the sides. Having that plank in place gave me something to fit the bottom planks to, so there isn’t a gap.
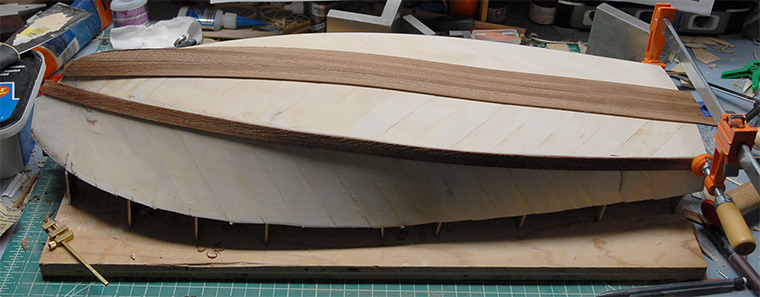
Below you can see the bottom planking done. The planks are just glued on with thick CA glue, so they go on fairly quickly.
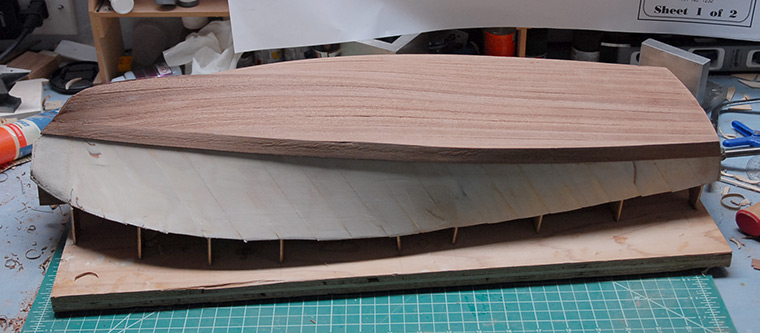
Below you can see a detail shot of the front. I wasn’t too careful about the fitment on these planks, as they will be below the waterline and therefore painted. With a little filler and sanding, this area will be nice and smooth before it gets painted.
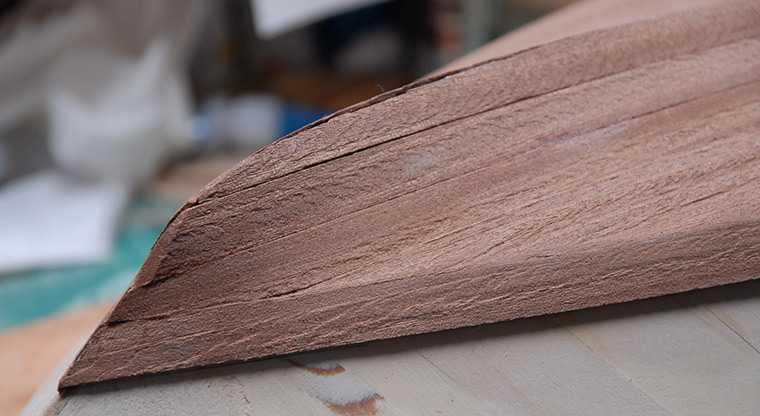
The planking continued on the sides of the boat. The planks were long enough to span the length of the boat, so attaching them really just consisted of tracing a line along the edge of each plank on the hull (seen below), and then using that line as a guide for where to apply some glue. With the glue in place, then I can just hold the plank in place until the glue sets.
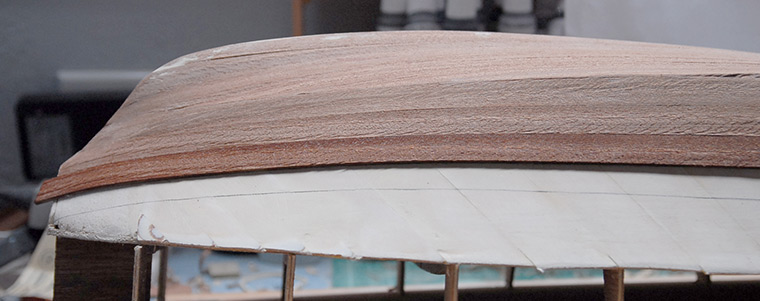
Below you can see all the bottom and side planks in place.
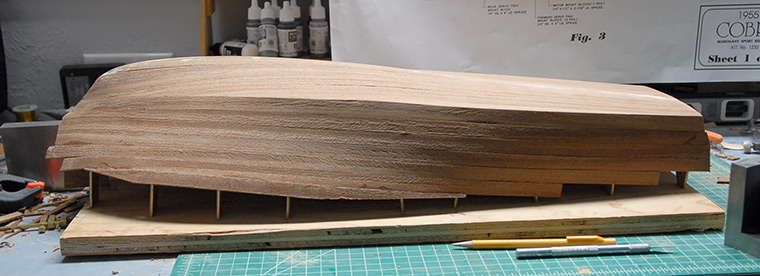
Here is a close-up showing the relatively rough surface of the planks. This will take quite a bit of sanding later to get it smoothed out.
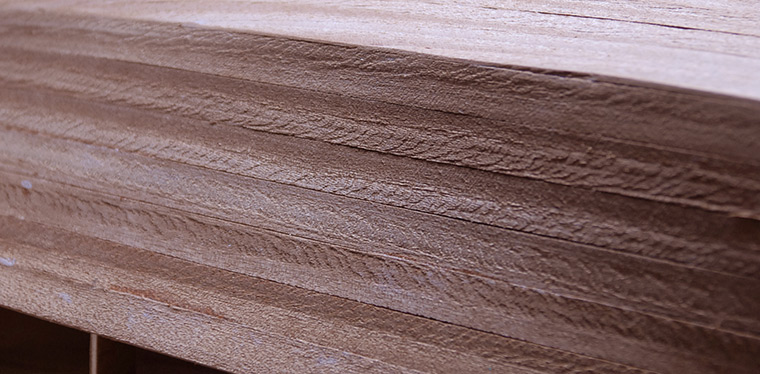
With all the planking in place, I applied a coat of the wood filler to the lower parts of the hull. This is the area that will later be painted, so having a smooth surface is more important than having good looking wood.
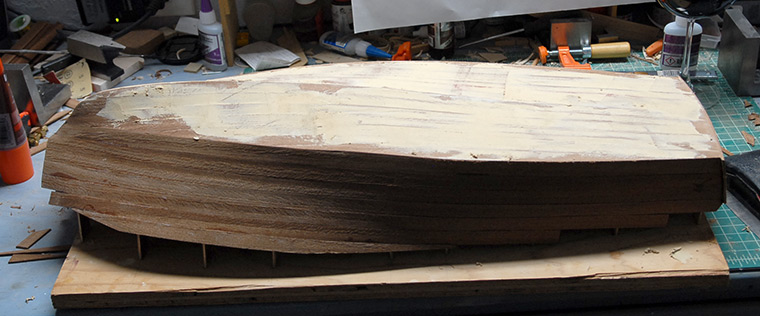
Below you can see the nose of the hull after a bit of sanding and refining of the center line.
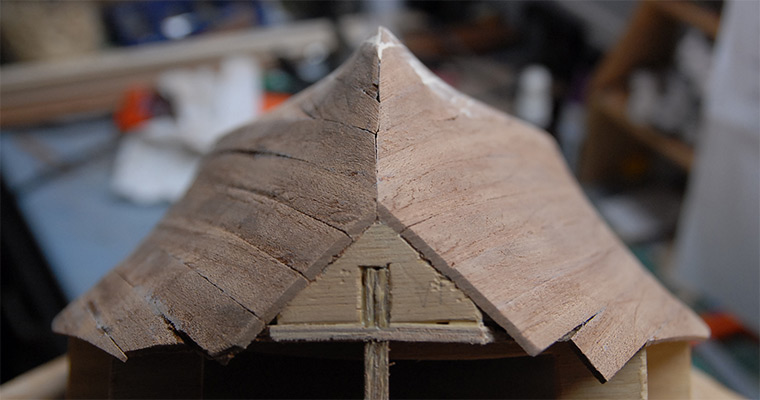
It was also at about this point that I realized that maybe soaking the big mahogany planks was not the best thing to do. It seems that while the planks being wet made them easier to bend around a few curves, it also made them swell just a bit. Once the planks had been on the hull for a few days and had dried out, they shrunk back to their original size, leaving a few gaps between the planks. I’m hoping that these will be filled in a bit later on, once I put a bunch of coats of spar varnish on the hull.

Next up was carving the nose from a block of mahogany. Below you can see the starting point, which was two triangles glued together, a mid point, when I had sawn off big chunks for rough shaping, and the point at which I had finished the rough shaping using a Dremel and sanding drum.
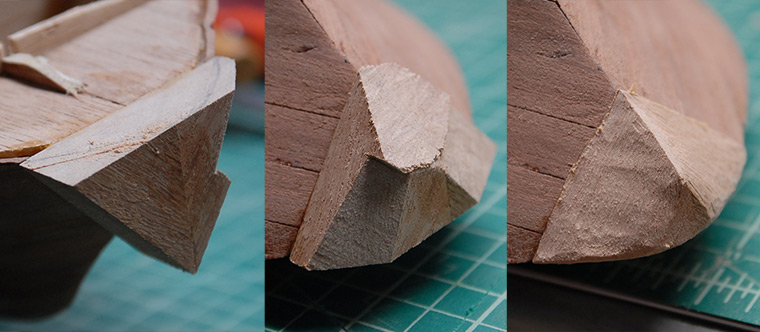
In order to reduce the mess from the sanding, I had some luck making a makeshift dust collection system using out vacuum cleaner hose positioned near the sanding. Below you can see an action shot of the sawdust coming off of the sanding drum and into the hose. It looked cool, so I took a photo :)
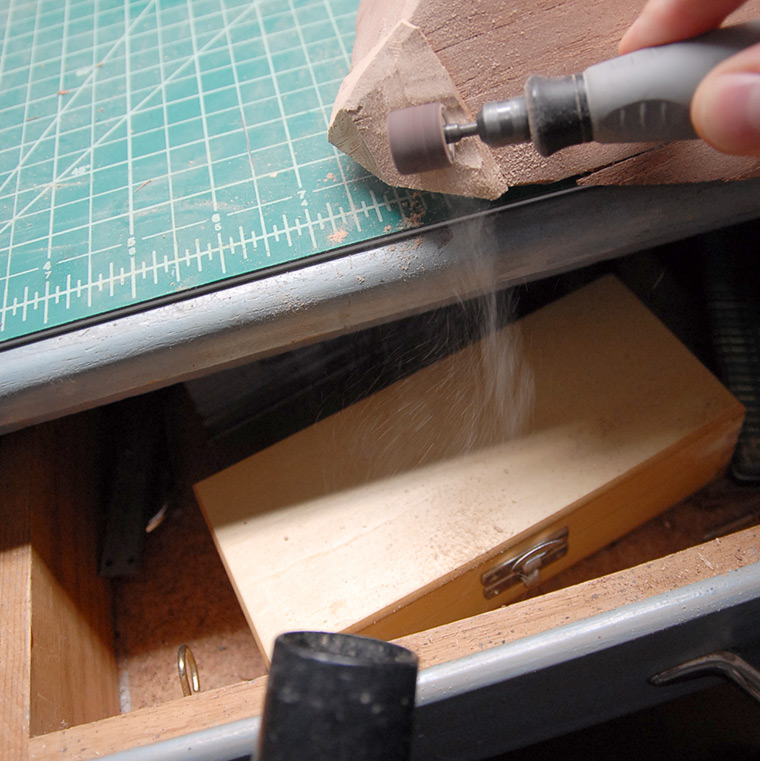
That completed the underside of the boat. The next step was to cut it off of the build board, sand the ribs flush with the top surface and then start adding the top deck components. Below you can see the edge parts glued in place. This was, unfortunately, where I made a bit of a mistake, placing the side strips a little bit too far inboard. I didn’t notice the misplacement until later in the build, though.
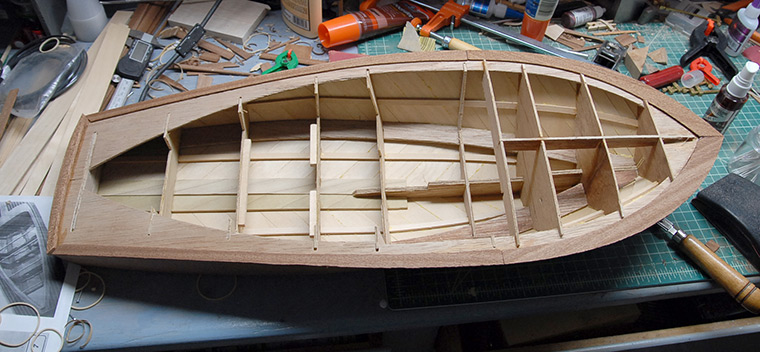
The side strips consist of three layers, each layer overlapping the others differently. Below you can see the second layer being held in place while the glue dries.

There is a strip that runs along the inside of the mahogany parts that provides support for the decking later. Below you can see it being glued in place.
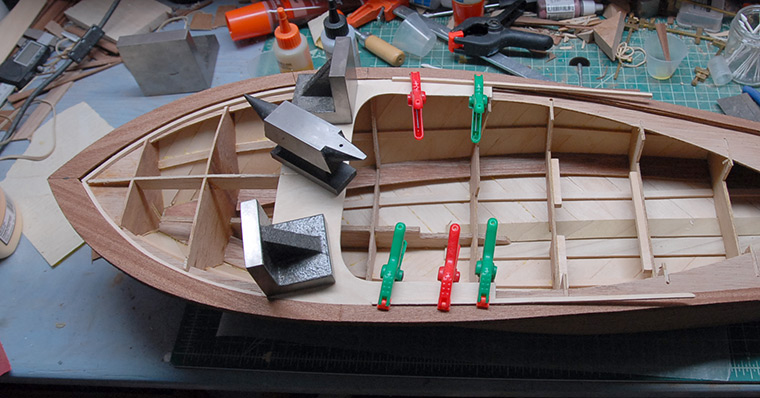
In gluing the above strip in place, I realized my mistake. The rear edge strip was in the correct place, but when I glued the side strips on, I had aligned the outside edges with the outside of the rear strip, when I SHOULD have aligned the inside edges. Once I discovered this, I found that I couldn’t pry off the side strips without doing lot of damage, so I opted instead to make adjustments to the build as I went, in order to compensate for the misalignment. The first thing I had to do was add a few extra strips to the back in order to even out the alignment of the inside edge. Below you can see the two additional strips, before sanding.
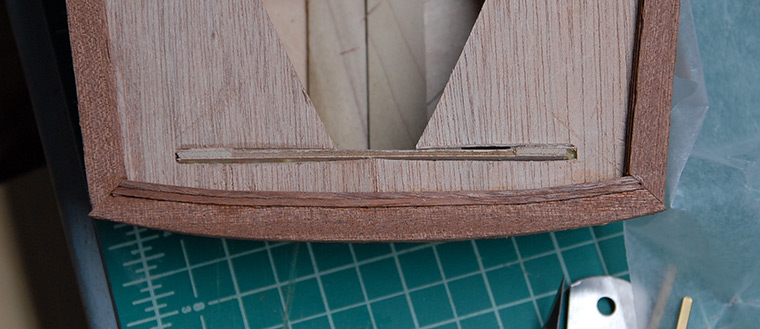
While there will need to be more adjustments later, the next few steps were fairly straightforward. Below you can see some decking glued in place, forming the front of the cockpit surround.
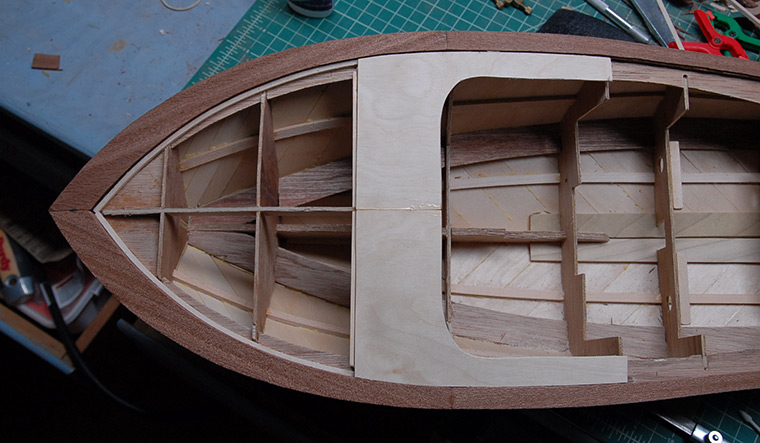
Front sub-planking in place, using the same techniques as the lower hull:
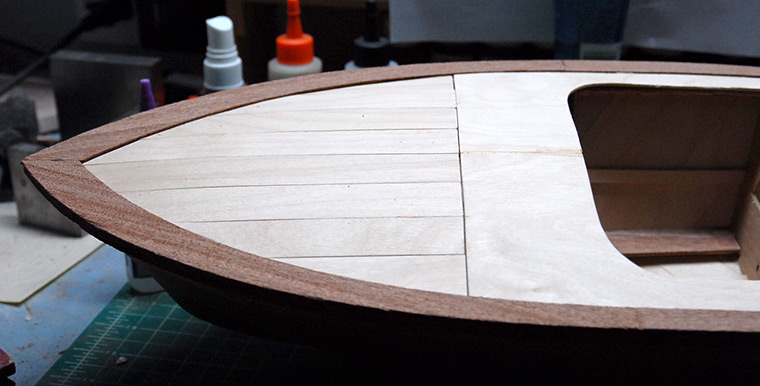
I order to provide support for the rear and side decks, I needed to add some support ribs. Theses were just 1/8” basswood, cut to length and tapered a bit so that there will be a bit of a slope to the decks.

Below you can see the side/rear sub-decking in place. I had to do a good deal of trimming and fitting to this piece in order to fit it into a space that is slightly smaller due to my additional thickness on the rear edge piece.
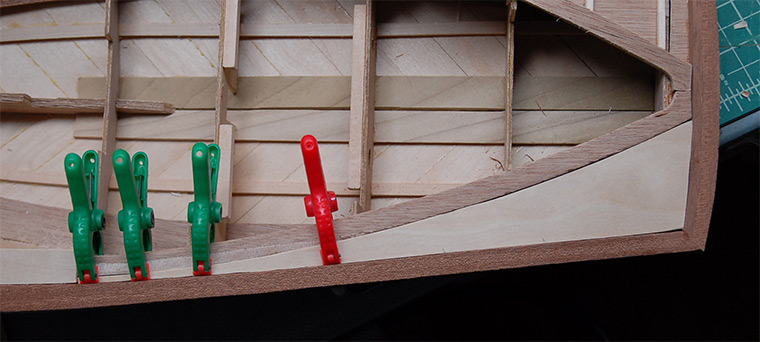
Finally, once the sub-deck was in place, I could start to add the final top decking layer. Below you can see the current state of the boat. Because the side rails should have been pushed just a bit back and out, the center basswood part didn’t reach the full length of the front deck. This meant that I had to add a little piece to extend it, which will be sanded and integrated more later. The thicker rear edge rail also required that the large basswood part be shortened slightly, in order to match up with the edges of the cockpit and still just meet the rear edge. I ended up removing approximately 1/4 inch from the straight section along the edge of the cockpit. I may also need to shorten the plastic molded pieces that form the engine cover and fin, but I was already thinking of cutting those up in order to add opening engine bay covers, so that may not cause any problems.
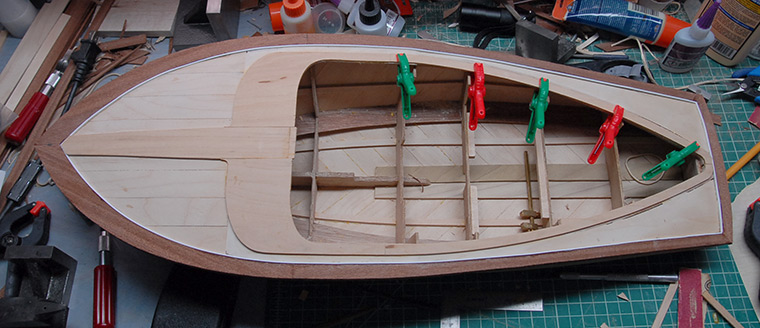
That is where the project stands now. Next up is applying the striped mahogany and plastic decking, and then a bunch of sanding to even it all out.
Thanks for reading!
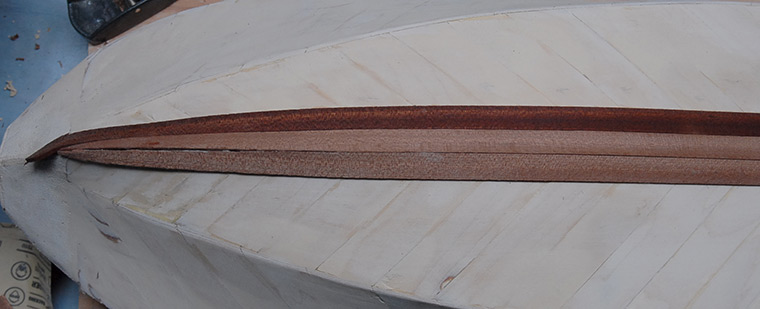
After a few rows of planks from the center, I then added one that runs along the edge that forms the border between the bottom and the sides. Having that plank in place gave me something to fit the bottom planks to, so there isn’t a gap.
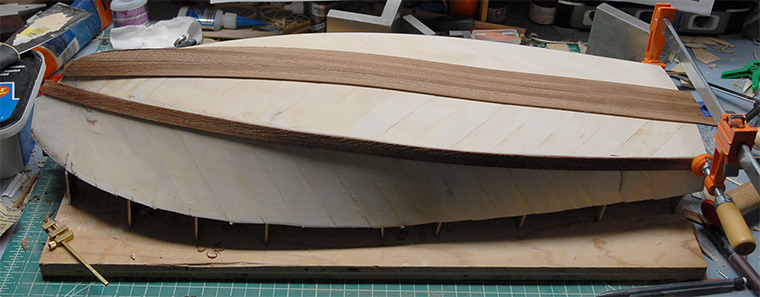
Below you can see the bottom planking done. The planks are just glued on with thick CA glue, so they go on fairly quickly.
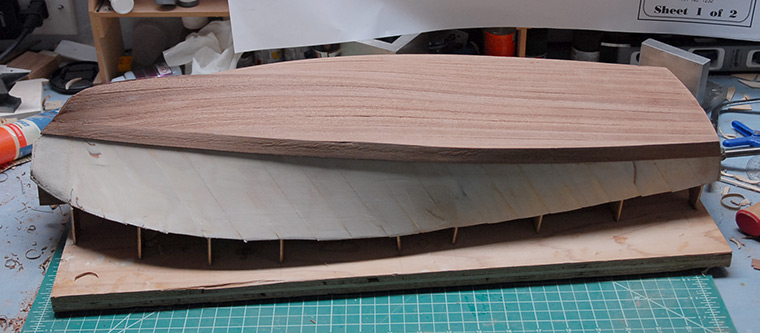
Below you can see a detail shot of the front. I wasn’t too careful about the fitment on these planks, as they will be below the waterline and therefore painted. With a little filler and sanding, this area will be nice and smooth before it gets painted.
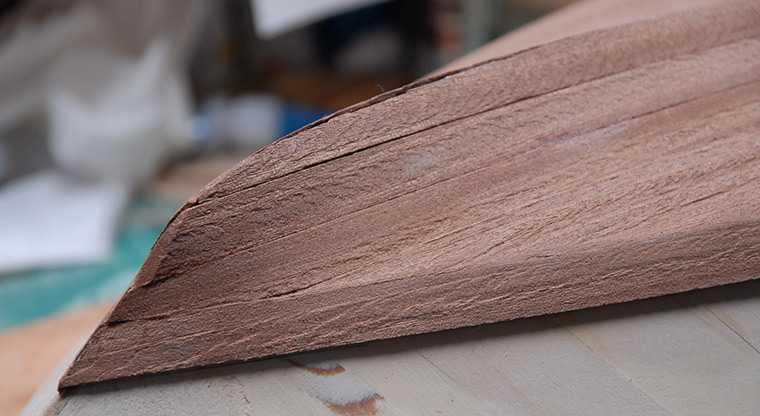
The planking continued on the sides of the boat. The planks were long enough to span the length of the boat, so attaching them really just consisted of tracing a line along the edge of each plank on the hull (seen below), and then using that line as a guide for where to apply some glue. With the glue in place, then I can just hold the plank in place until the glue sets.
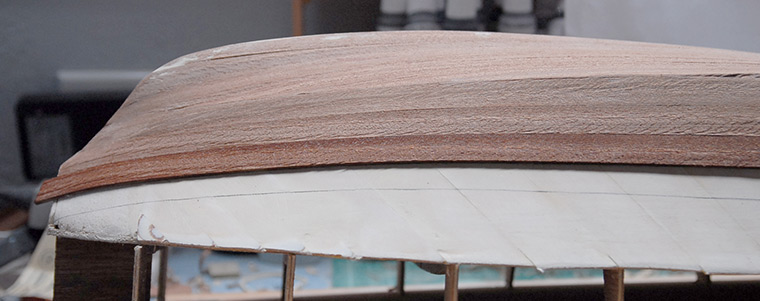
Below you can see all the bottom and side planks in place.
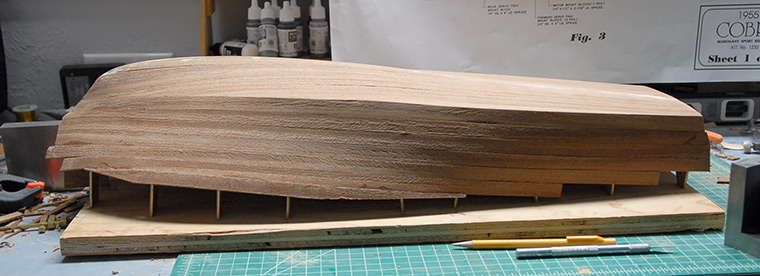
Here is a close-up showing the relatively rough surface of the planks. This will take quite a bit of sanding later to get it smoothed out.
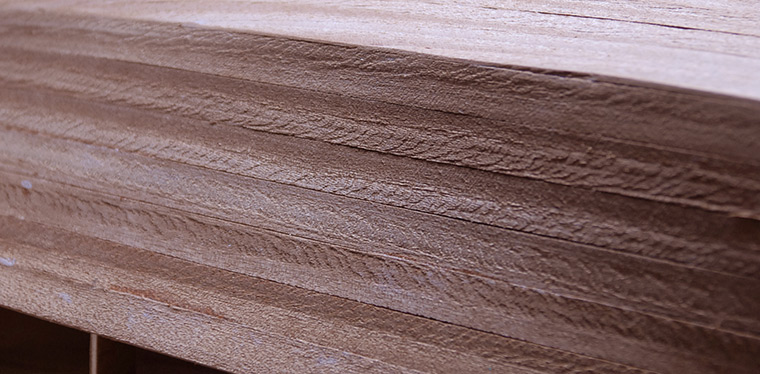
With all the planking in place, I applied a coat of the wood filler to the lower parts of the hull. This is the area that will later be painted, so having a smooth surface is more important than having good looking wood.
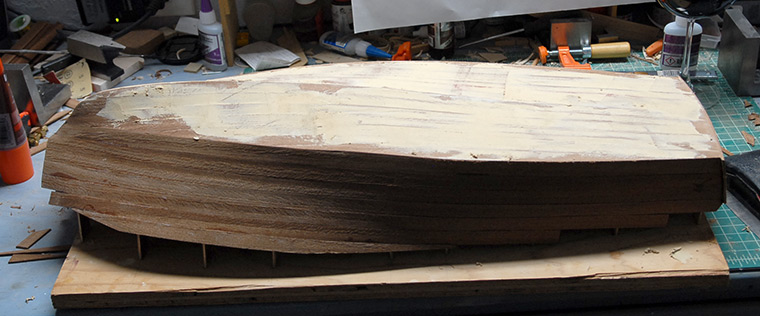
Below you can see the nose of the hull after a bit of sanding and refining of the center line.
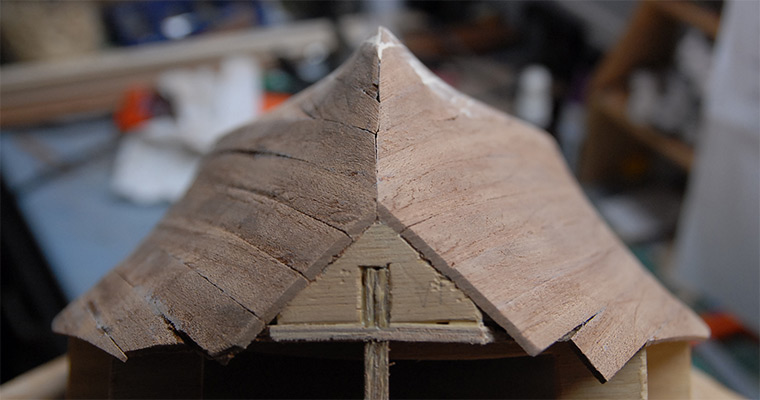
It was also at about this point that I realized that maybe soaking the big mahogany planks was not the best thing to do. It seems that while the planks being wet made them easier to bend around a few curves, it also made them swell just a bit. Once the planks had been on the hull for a few days and had dried out, they shrunk back to their original size, leaving a few gaps between the planks. I’m hoping that these will be filled in a bit later on, once I put a bunch of coats of spar varnish on the hull.

Next up was carving the nose from a block of mahogany. Below you can see the starting point, which was two triangles glued together, a mid point, when I had sawn off big chunks for rough shaping, and the point at which I had finished the rough shaping using a Dremel and sanding drum.
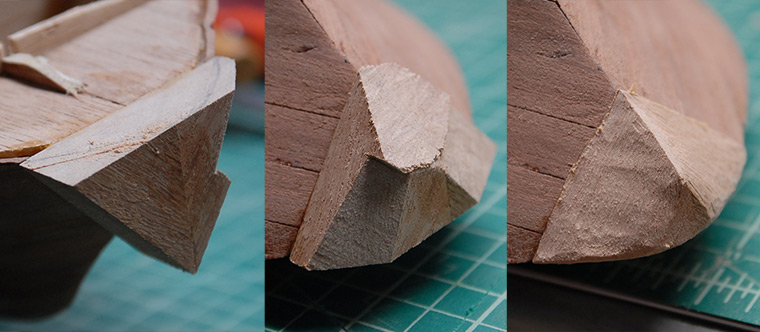
In order to reduce the mess from the sanding, I had some luck making a makeshift dust collection system using out vacuum cleaner hose positioned near the sanding. Below you can see an action shot of the sawdust coming off of the sanding drum and into the hose. It looked cool, so I took a photo :)
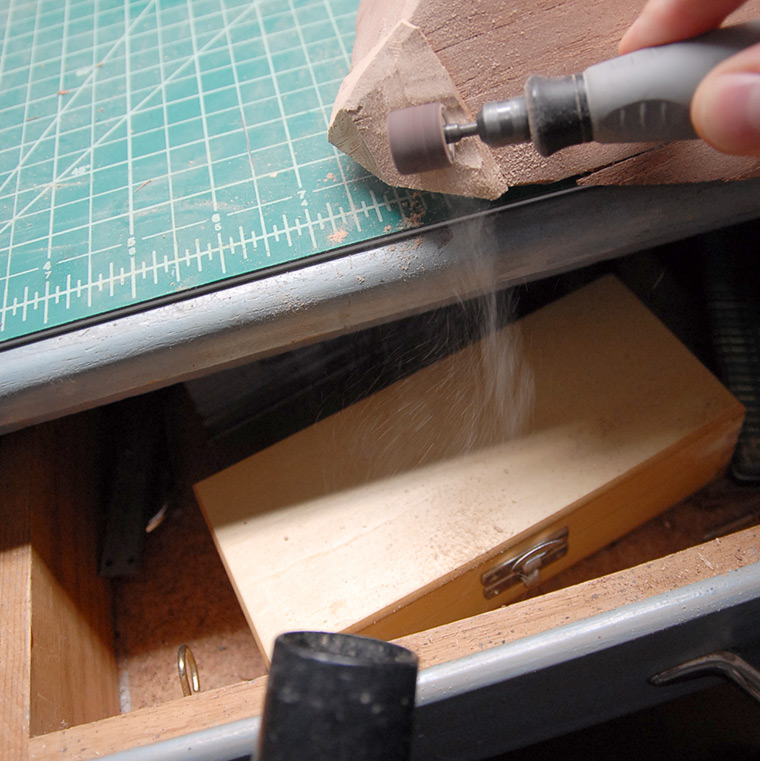
That completed the underside of the boat. The next step was to cut it off of the build board, sand the ribs flush with the top surface and then start adding the top deck components. Below you can see the edge parts glued in place. This was, unfortunately, where I made a bit of a mistake, placing the side strips a little bit too far inboard. I didn’t notice the misplacement until later in the build, though.
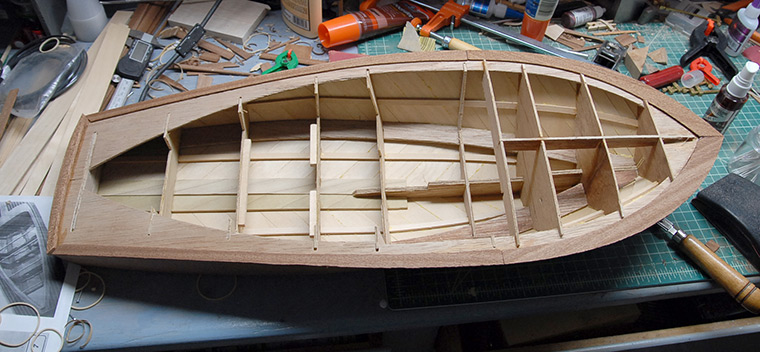
The side strips consist of three layers, each layer overlapping the others differently. Below you can see the second layer being held in place while the glue dries.

There is a strip that runs along the inside of the mahogany parts that provides support for the decking later. Below you can see it being glued in place.
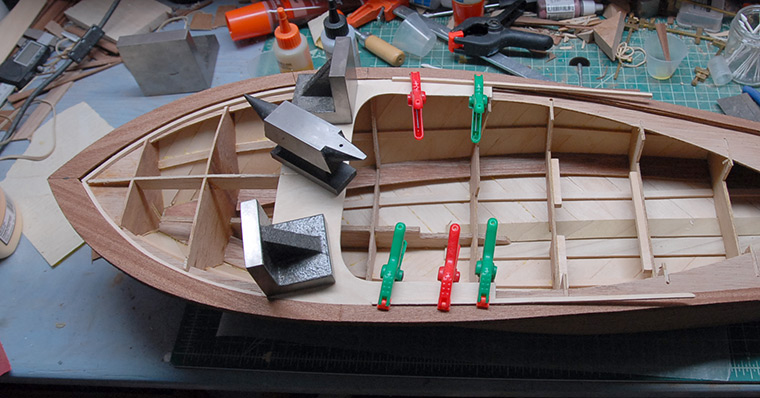
In gluing the above strip in place, I realized my mistake. The rear edge strip was in the correct place, but when I glued the side strips on, I had aligned the outside edges with the outside of the rear strip, when I SHOULD have aligned the inside edges. Once I discovered this, I found that I couldn’t pry off the side strips without doing lot of damage, so I opted instead to make adjustments to the build as I went, in order to compensate for the misalignment. The first thing I had to do was add a few extra strips to the back in order to even out the alignment of the inside edge. Below you can see the two additional strips, before sanding.
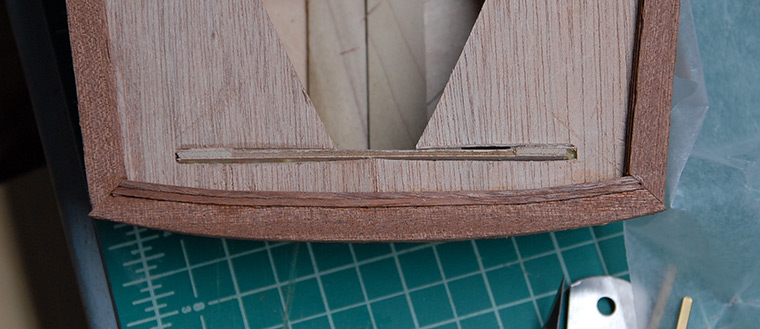
While there will need to be more adjustments later, the next few steps were fairly straightforward. Below you can see some decking glued in place, forming the front of the cockpit surround.
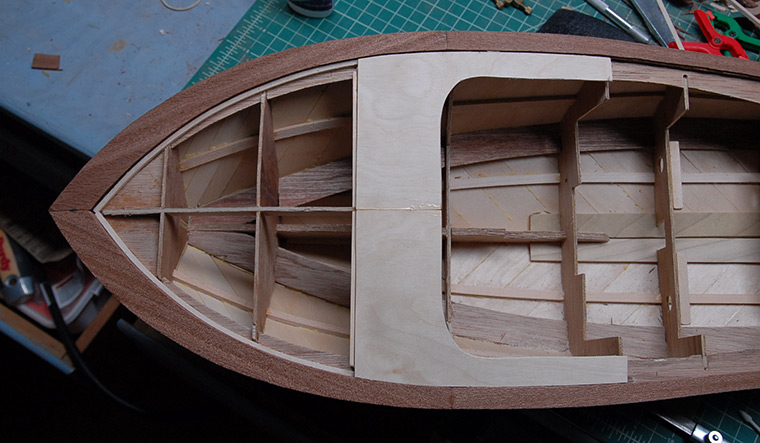
Front sub-planking in place, using the same techniques as the lower hull:
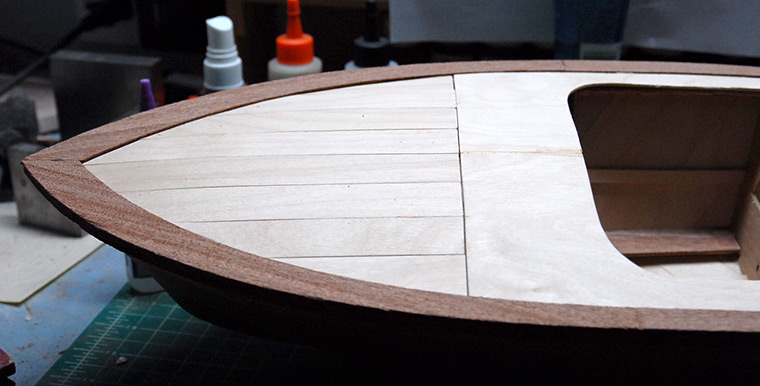
I order to provide support for the rear and side decks, I needed to add some support ribs. Theses were just 1/8” basswood, cut to length and tapered a bit so that there will be a bit of a slope to the decks.

Below you can see the side/rear sub-decking in place. I had to do a good deal of trimming and fitting to this piece in order to fit it into a space that is slightly smaller due to my additional thickness on the rear edge piece.
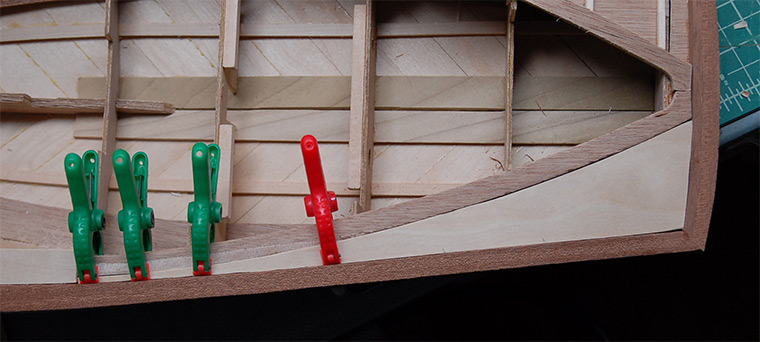
Finally, once the sub-deck was in place, I could start to add the final top decking layer. Below you can see the current state of the boat. Because the side rails should have been pushed just a bit back and out, the center basswood part didn’t reach the full length of the front deck. This meant that I had to add a little piece to extend it, which will be sanded and integrated more later. The thicker rear edge rail also required that the large basswood part be shortened slightly, in order to match up with the edges of the cockpit and still just meet the rear edge. I ended up removing approximately 1/4 inch from the straight section along the edge of the cockpit. I may also need to shorten the plastic molded pieces that form the engine cover and fin, but I was already thinking of cutting those up in order to add opening engine bay covers, so that may not cause any problems.
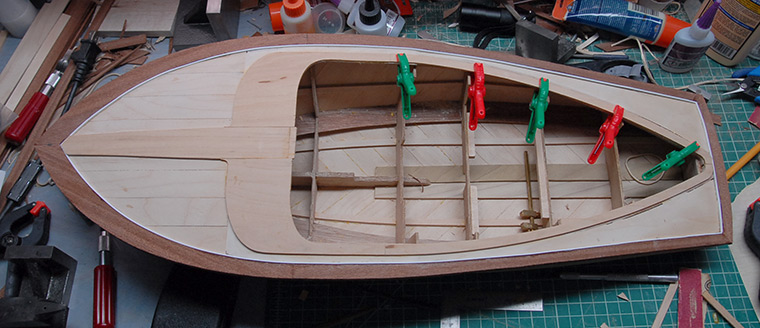
That is where the project stands now. Next up is applying the striped mahogany and plastic decking, and then a bunch of sanding to even it all out.
Thanks for reading!
1955 Chris-Craft Cobra
15 - May - 2016 - 21:47
Back at the end of 2015, I was in Orlando, Florida, visiting Disney World (taking advantage of a perk of working for the mouse: free park entry!). One of the restaurants in Disney Springs (formerly Downtown Disney) was just FILLED with great looking large scale boat and ship models. I was inspired to take up a wooden model project again, except this time I wanted it to end up shiny. After a bit of research, I narrowed it down to a handful of possible kit options. Mostly I was looking at kits from Dumas, as they have some great looking Chris-Craft speedboat kits. I spent a Saturday morning making the rounds at my local hobby shops (living in the SF Bay Area, there are a few to choose from) and managed to find this kit:
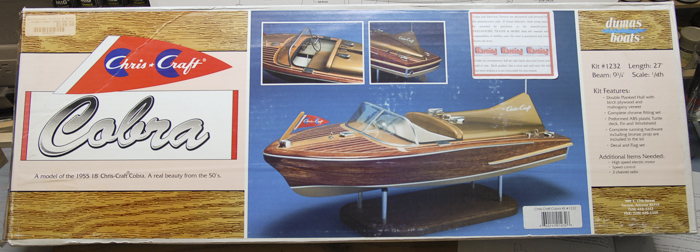
With a length of 27 inches, it’s a fairly large scale project (at least for me and my limited building space).
Like most kits of this type, it comes as a number of sheets of pre-cut parts, some strips of thin plywood, a bunch of strips of mahogany and bass wood, and some cast metal parts.
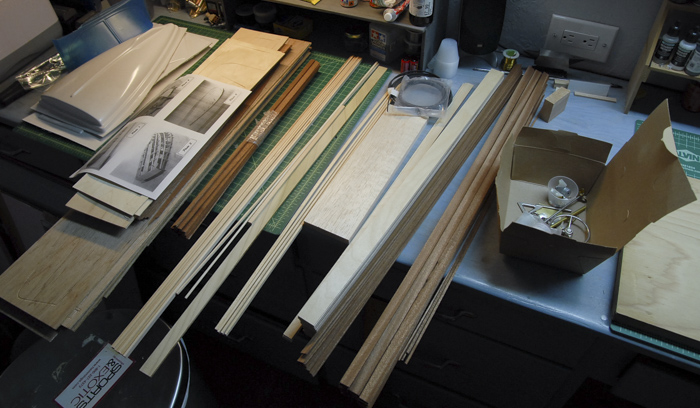
The instructions had me start by marking rib positions on a building board (spare plywood in this case) and then assembling and gluing the frame to the board.
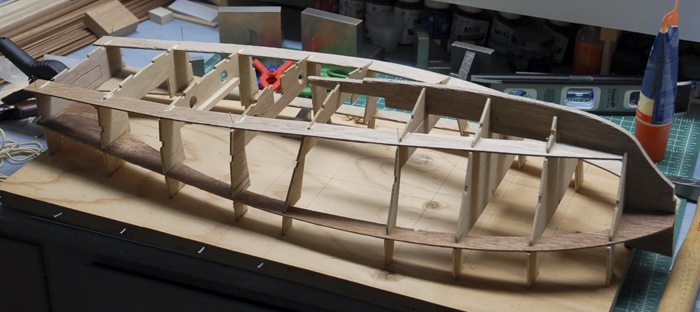
That was followed by adding a few stringers and the keel boards on the bottom of the boat.
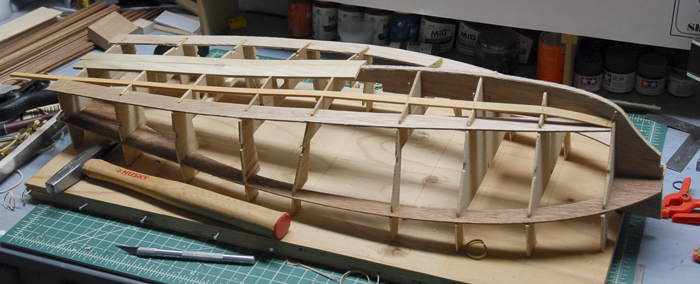
Because of the rapid change in shape between the first rib and the nose of the boat, the front is shaped from balsa. The kit came with a sheet of half-inch-thick balsa that was cut into triangles and glued in place. Below you can see the rough blocks glued in place. I had to use a little bit of spare balsa that I had laying around in order to fill the space all of the way (those thin sheets right at the front).
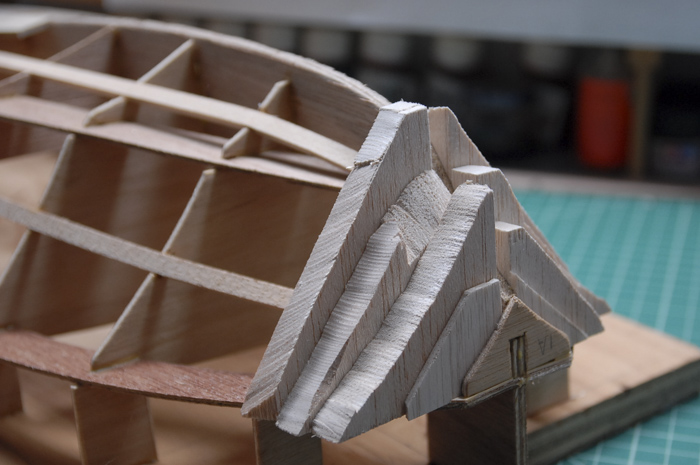
Below you can see the rough shaping. This was done using first a jewelers saw to cut off big chunks of the wood, then a sanding drum on a Dremel for fast shaping and then finally some 150 grit sandpaper for finer shaping.
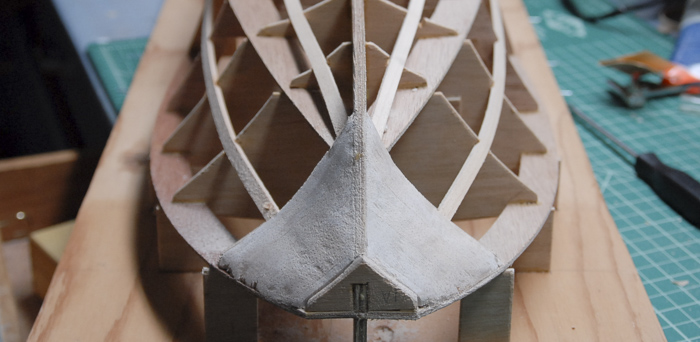
Next up was the under-planking. This consisted of 1/16 inch thick plywood strips that are laid diagonally on the bottom and sides of the hull. The instructions said to use a thick cyanoacrylate (super glue), but I found that when the strips needed to be bent a bit, the glue tended to not have the strength to hold the strips in place. I believe that this was mostly because there were fairly small areas in which the strips contacted the frame. I had actually started the planking and then found that I had started laying the planks going the wrong direction (dark spots in photo below was the glue that held them in place). When I discovered this, I tried to take those planks off and discovered that they came off so easily that I lost all confidence in the CA method.
I decided instead to try good ol’ yellow carpenter’s glue. This required that the strips be clamped in place while the glue dried. Once dried, though, the glue was strong and the connection between the strips and frame was solid. I ended up going with this technique for all of the under-planking. Below you can see the transom in place as well as the first few planks.
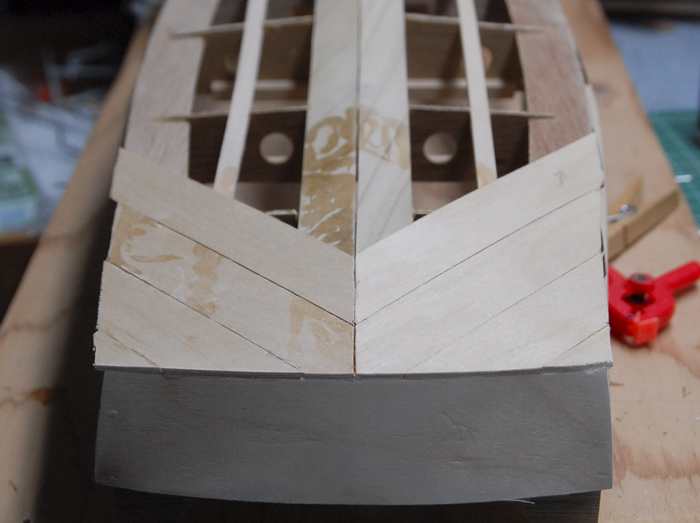
Below you can see some of the clamping and weighting I needed to do in order to hold planks in place while the glue dried. Those angle blocks weigh 3lbs each, and were providing a great deal of pressure on those planks.
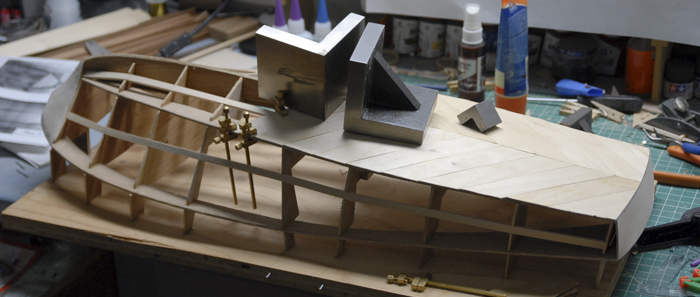
A closer view of the same setup.
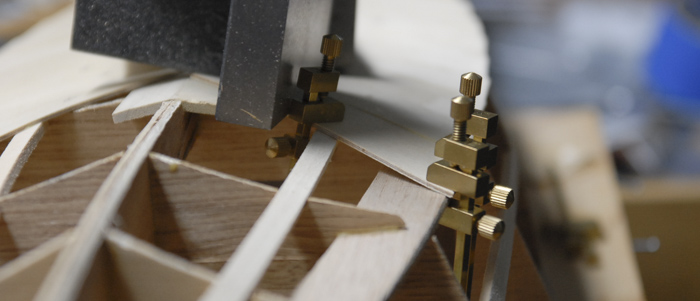
As I got closer and closer to the nose of the boat, the angle between the bottom planks and the chine (frame piece that is the line between the sides and bottom) became shallower and the area of contact between the two got smaller. What I decided to do was add a few strips of basswood, trimmed to the correct angle, in order to give more contact area. Below you can see those strips in place.
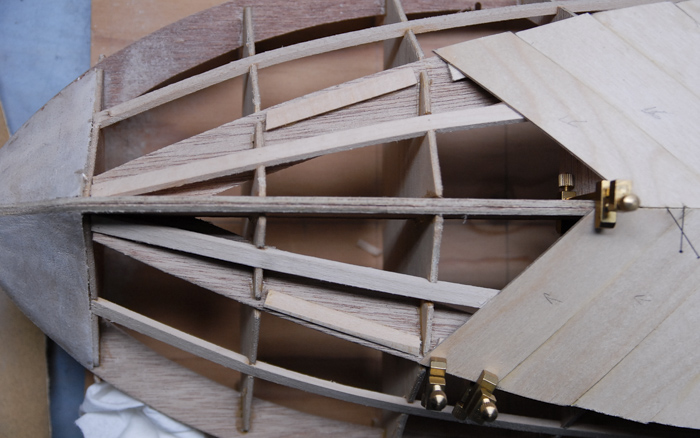
A different angle on the same strips. You can see that the left side is untrimmed, while the right side is trimmed to the angle of the strips of plywood.
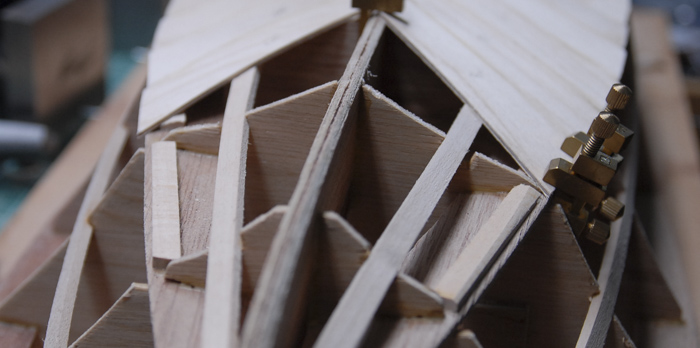
Below you can see the entire bottom of the boat with under-planking on it. The top edge in this photo has been sanded even with the angle of the side, while the bottom edge still looks ragged because it has not yet been sanded smooth.
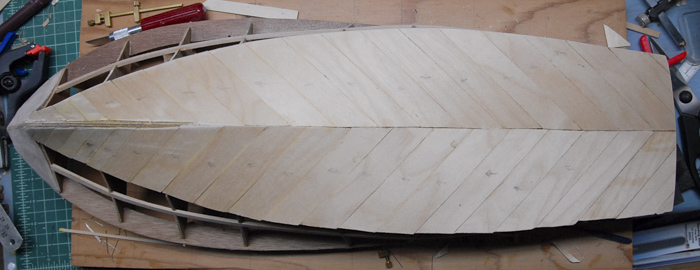
The planking of the sides was very similar. I did attempt to use straight sewing pins as temporary nails. This worked some times and other times just resulted in lots of bent pins and plenty of cursing.
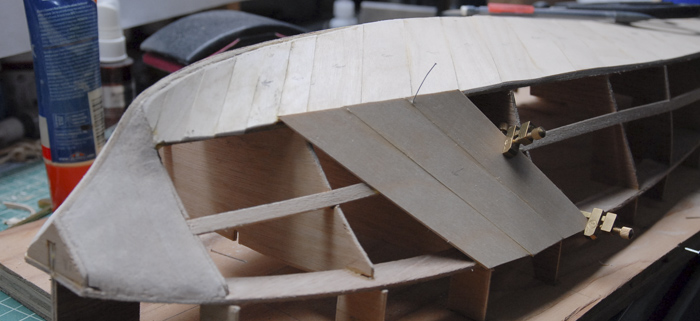
Using thinner strips of plywood near the front. The thinner strips are easier to bend and can therefore be formed to the sharper curves near the bow.
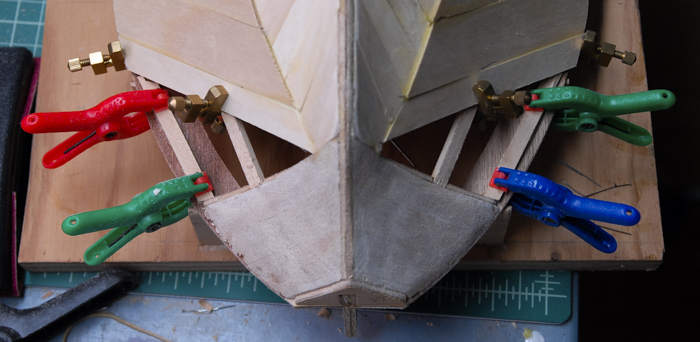
With the under-planking complete, the whole hull got a first pass of sanding.
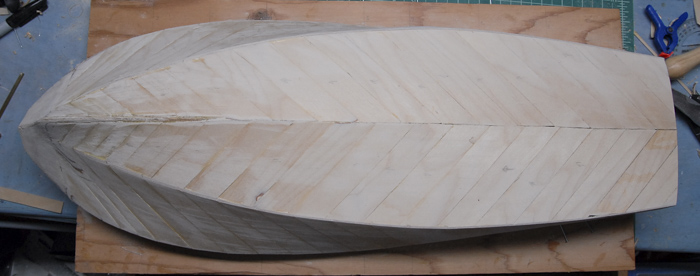
In a few places, a plank or two ended up lower than I would like. In the case below, I added another bit of strip on top and then sanded it flush to the surrounding planks.
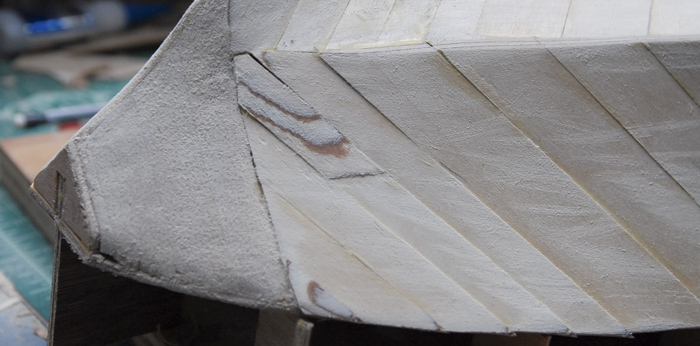
After that first pass of sanding, I put a thin layer of wood filler over most of the hull. This filled in gaps, leveled out the surface and gave me something to sand down in order to get things nice and smooth before the top plank layer.
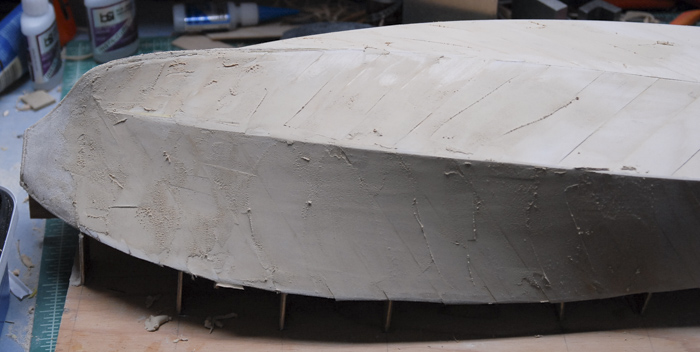
Below you can see the filled and sanded result, all ready for the mahogany plank layer.
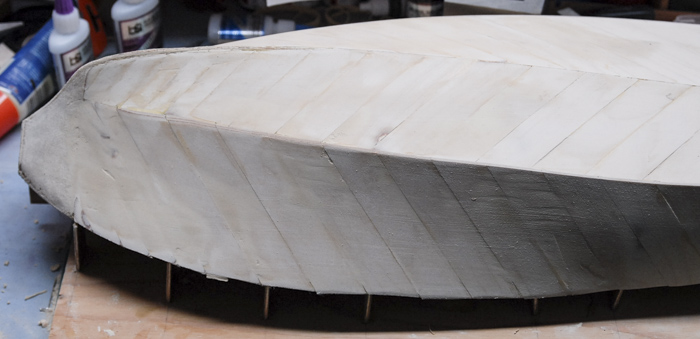
That seems like a good place to stop for this post. The mahogany planking is nearly done, so look for that in a forthcoming blog post!
Thanks for reading!
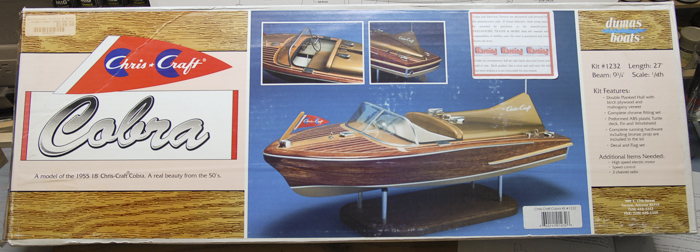
With a length of 27 inches, it’s a fairly large scale project (at least for me and my limited building space).
Like most kits of this type, it comes as a number of sheets of pre-cut parts, some strips of thin plywood, a bunch of strips of mahogany and bass wood, and some cast metal parts.
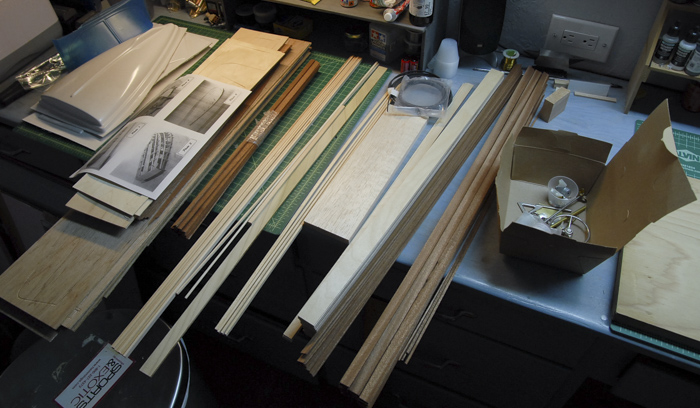
The instructions had me start by marking rib positions on a building board (spare plywood in this case) and then assembling and gluing the frame to the board.
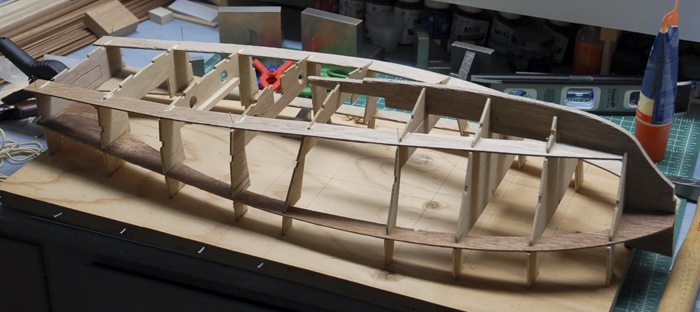
That was followed by adding a few stringers and the keel boards on the bottom of the boat.
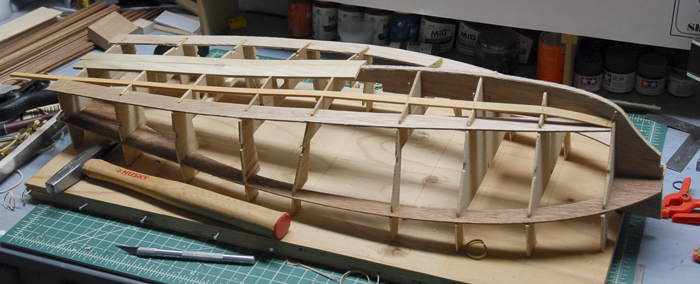
Because of the rapid change in shape between the first rib and the nose of the boat, the front is shaped from balsa. The kit came with a sheet of half-inch-thick balsa that was cut into triangles and glued in place. Below you can see the rough blocks glued in place. I had to use a little bit of spare balsa that I had laying around in order to fill the space all of the way (those thin sheets right at the front).
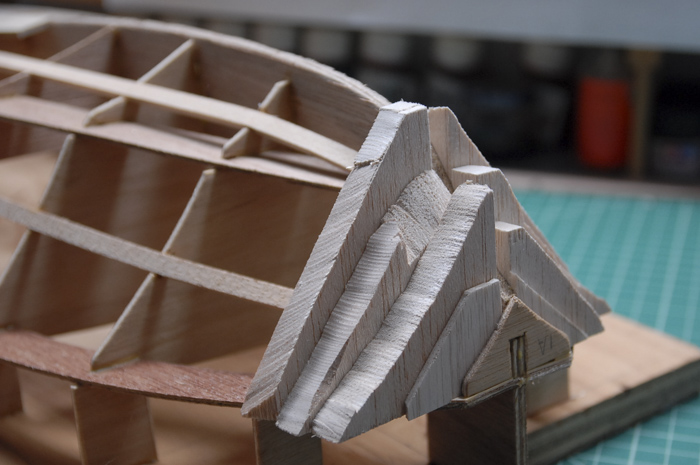
Below you can see the rough shaping. This was done using first a jewelers saw to cut off big chunks of the wood, then a sanding drum on a Dremel for fast shaping and then finally some 150 grit sandpaper for finer shaping.
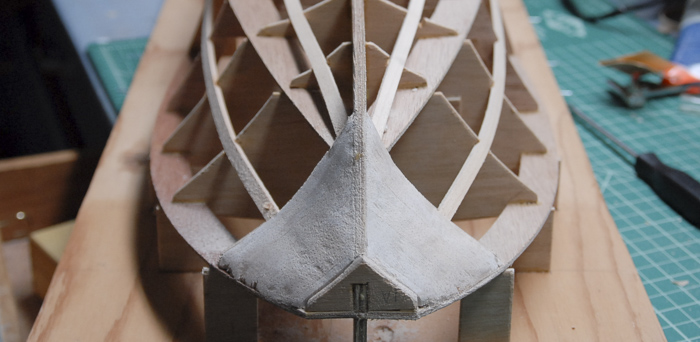
Next up was the under-planking. This consisted of 1/16 inch thick plywood strips that are laid diagonally on the bottom and sides of the hull. The instructions said to use a thick cyanoacrylate (super glue), but I found that when the strips needed to be bent a bit, the glue tended to not have the strength to hold the strips in place. I believe that this was mostly because there were fairly small areas in which the strips contacted the frame. I had actually started the planking and then found that I had started laying the planks going the wrong direction (dark spots in photo below was the glue that held them in place). When I discovered this, I tried to take those planks off and discovered that they came off so easily that I lost all confidence in the CA method.
I decided instead to try good ol’ yellow carpenter’s glue. This required that the strips be clamped in place while the glue dried. Once dried, though, the glue was strong and the connection between the strips and frame was solid. I ended up going with this technique for all of the under-planking. Below you can see the transom in place as well as the first few planks.
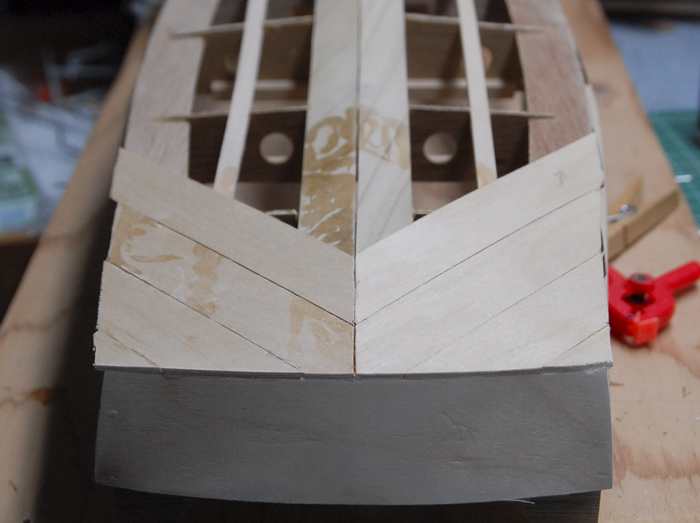
Below you can see some of the clamping and weighting I needed to do in order to hold planks in place while the glue dried. Those angle blocks weigh 3lbs each, and were providing a great deal of pressure on those planks.
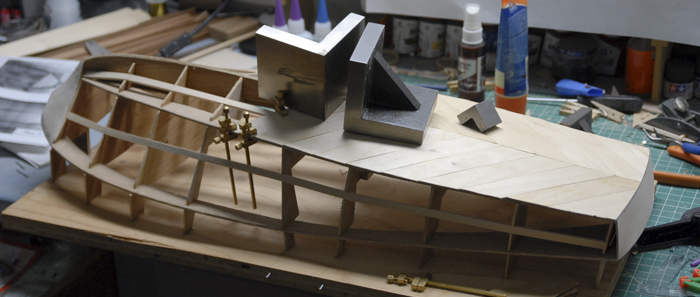
A closer view of the same setup.
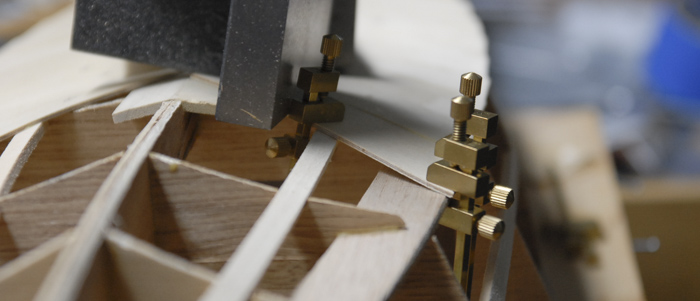
As I got closer and closer to the nose of the boat, the angle between the bottom planks and the chine (frame piece that is the line between the sides and bottom) became shallower and the area of contact between the two got smaller. What I decided to do was add a few strips of basswood, trimmed to the correct angle, in order to give more contact area. Below you can see those strips in place.
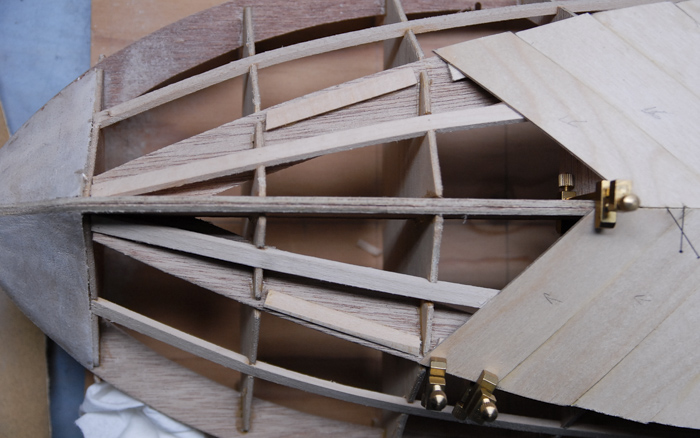
A different angle on the same strips. You can see that the left side is untrimmed, while the right side is trimmed to the angle of the strips of plywood.
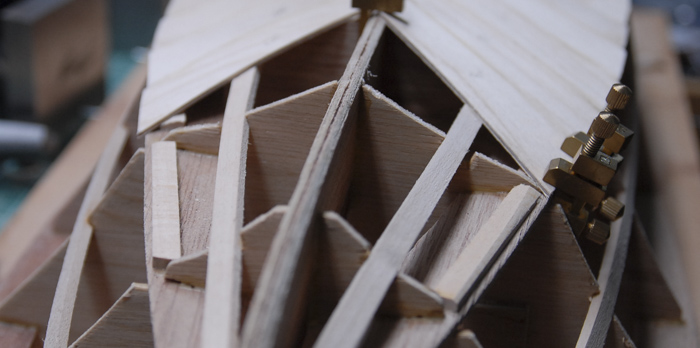
Below you can see the entire bottom of the boat with under-planking on it. The top edge in this photo has been sanded even with the angle of the side, while the bottom edge still looks ragged because it has not yet been sanded smooth.
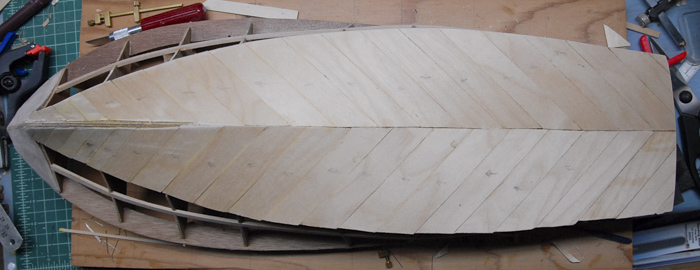
The planking of the sides was very similar. I did attempt to use straight sewing pins as temporary nails. This worked some times and other times just resulted in lots of bent pins and plenty of cursing.
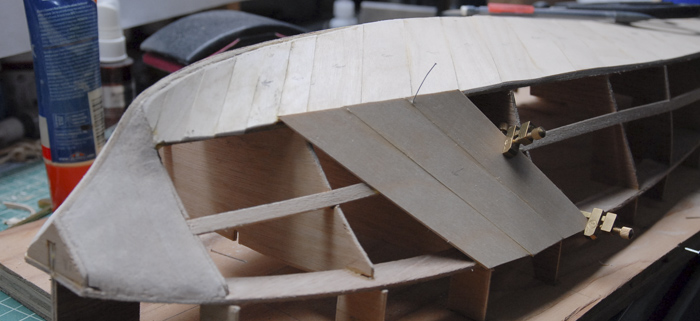
Using thinner strips of plywood near the front. The thinner strips are easier to bend and can therefore be formed to the sharper curves near the bow.
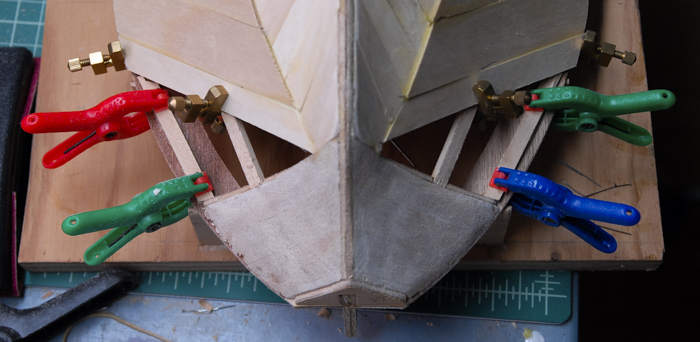
With the under-planking complete, the whole hull got a first pass of sanding.
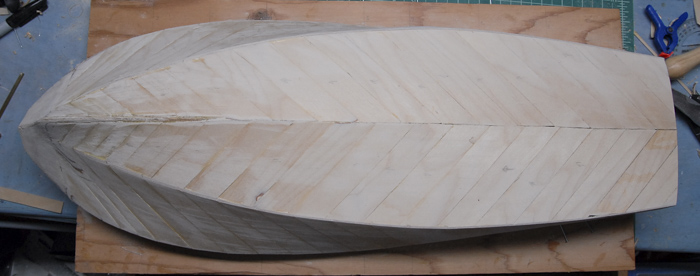
In a few places, a plank or two ended up lower than I would like. In the case below, I added another bit of strip on top and then sanded it flush to the surrounding planks.
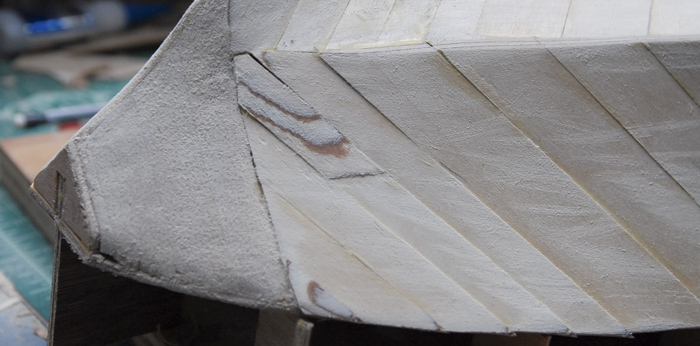
After that first pass of sanding, I put a thin layer of wood filler over most of the hull. This filled in gaps, leveled out the surface and gave me something to sand down in order to get things nice and smooth before the top plank layer.
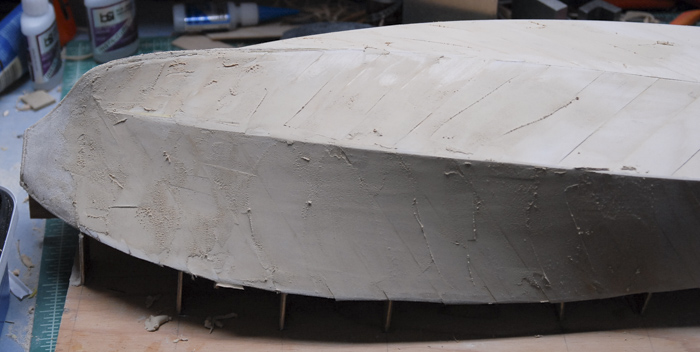
Below you can see the filled and sanded result, all ready for the mahogany plank layer.
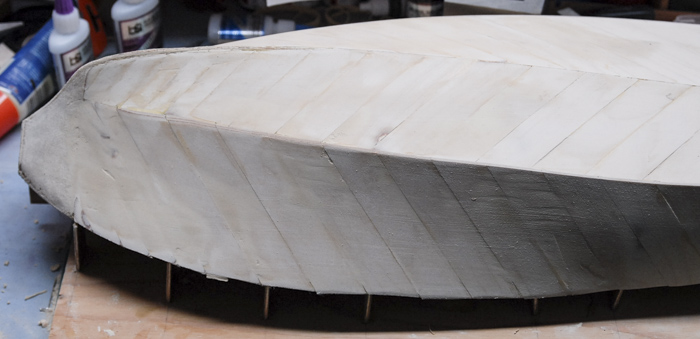
That seems like a good place to stop for this post. The mahogany planking is nearly done, so look for that in a forthcoming blog post!
Thanks for reading!
1930 Chris Craft Runabout in 1/24 scale
19 - February - 2009 - 21:15
Here are a few images of the last model I finished. This was the first model that I have ever done that had a finished wood construction. When I was a kid I had done a few of the little balsa airplanes that have a tissue out surface, but this boat was a totally different beast.
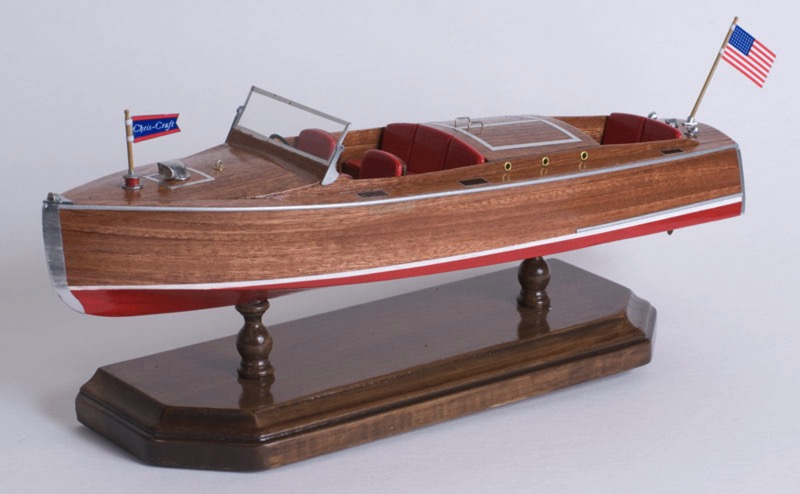
This kit is a Dumas Boats 1930 Chris Craft Runabout at 1/24 scale. The finished product is about 12" long. It's got a balsa frame and underplanking, with mahogany final planking.
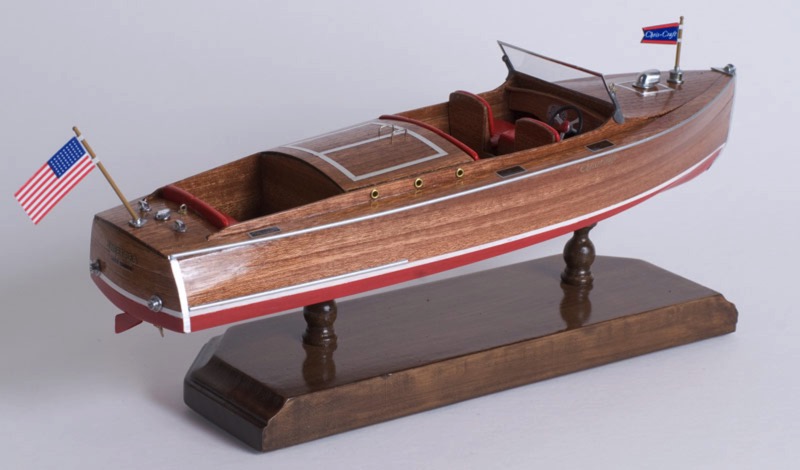
Previous to this kit, almost all of the kits I have built have been plastic. This meant the emphasis was far and away on the painting and cleanup of the plastic. A little filler here, some shading and weathering there and the kits come out nice. This, on the other hand, was a good deal more about the construction, with hardly any painting at all. There was a great deal of shaping and sanding of the raw planks of wood, which, while making a saw-dusty mess of my office, made me feel much more like I had actually BUILT the model, rather than just assembled a kit. There was also a bit of metal cleanup and polishing on the white metal parts, and some working with materials I had not dealt with before (sheet adhesive aluminum).
Overall, I learned quite a bit and whet my appetite for further exploration into the ship building process. As a result, I decided to order up a new ship model (see previous post), with a good deal more complexity, and give that a try.
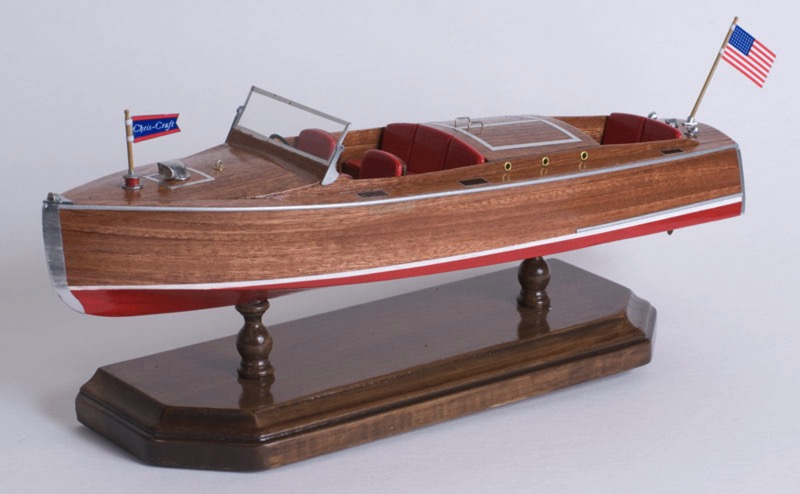
This kit is a Dumas Boats 1930 Chris Craft Runabout at 1/24 scale. The finished product is about 12" long. It's got a balsa frame and underplanking, with mahogany final planking.
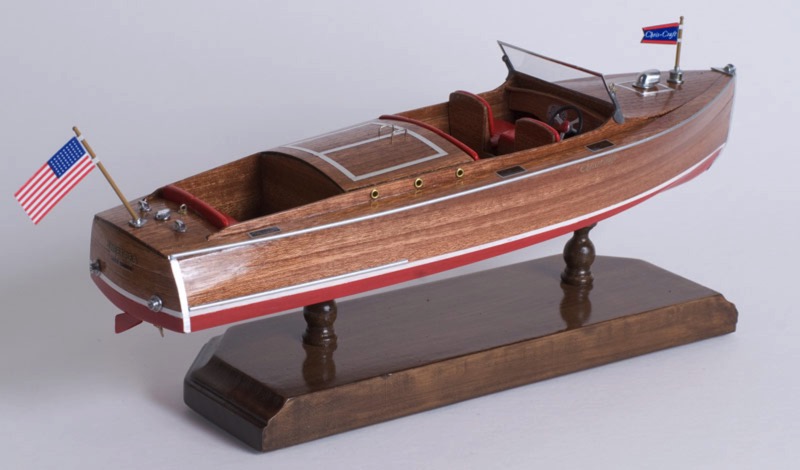
Previous to this kit, almost all of the kits I have built have been plastic. This meant the emphasis was far and away on the painting and cleanup of the plastic. A little filler here, some shading and weathering there and the kits come out nice. This, on the other hand, was a good deal more about the construction, with hardly any painting at all. There was a great deal of shaping and sanding of the raw planks of wood, which, while making a saw-dusty mess of my office, made me feel much more like I had actually BUILT the model, rather than just assembled a kit. There was also a bit of metal cleanup and polishing on the white metal parts, and some working with materials I had not dealt with before (sheet adhesive aluminum).
Overall, I learned quite a bit and whet my appetite for further exploration into the ship building process. As a result, I decided to order up a new ship model (see previous post), with a good deal more complexity, and give that a try.